China Robots Displace Workers as Wage Spiral Pressures Profits
- gtbmsbcs
- 2017年7月3日
- 讀畢需時 3 分鐘
Study finds average factory wages doubling over 10 years
Companies are tapping subsidies, tax breaks, and automating

As he marches through a gritty factory that makes baby strollers and wheels, Hu Chengpeng says finding workers is his number one challenge these days. Turnover at the facility in Hanchuan in Hubei province in central China is running at 20 percent, even while wages have been growing by double digits for his 400-plus workers every year. “Labor costs are getting just too high,” he said.
All of which explains why Hu, 34, is embracing China’s robotics revolution. He has added 40 new robots, each costing 40,000 yuan ($5,850), this year to replace dozens of workers tasked with cutting plastic molding. Eventually the factory will use a quarter fewer workers than today, without having to reduce annual production, he said. Hu also said he plans to shift more production away from making simple components and towards producing higher-margin branded strollers.
With real wages more than doubling in the last decade, manufacturers are automating, investing in research and development, and adding new higher-value products, according to the latest findings of the China Employer-Employee Survey (CEES), carried out by the Wuhan University Institute of Quality Development Strategy, Chinese Academy of Social Sciences, Stanford University, and the HKUST Institute for Emerging Market Studies.
China is no longer the cheap labor haven it once was. Monthly manufacturing wages reached 4,126 yuan at the end of 2015, equal to those in Brazil but much higher than Mexico, Thailand, Malaysia, Vietnam, and India.
At the same time, many firms are relying on government subsidies, while barely eking out profits or even losing money, according to the study released June 20. “Time is running out fast for Chinese manufacturers to adapt,” says Albert Park, head of the survey’s international committee and a labor economist at The Hong Kong University of Science and Technology.
The study canvassed more than 1,200 companies and 11,300 workers in Guangdong, China’s biggest manufacturing province, and Hubei, a major industrial base in central China. Some 26 percent of workers left their jobs annually in Guangdong and that turnover rate was even higher for younger workers, about 37 percent for employees below 28.
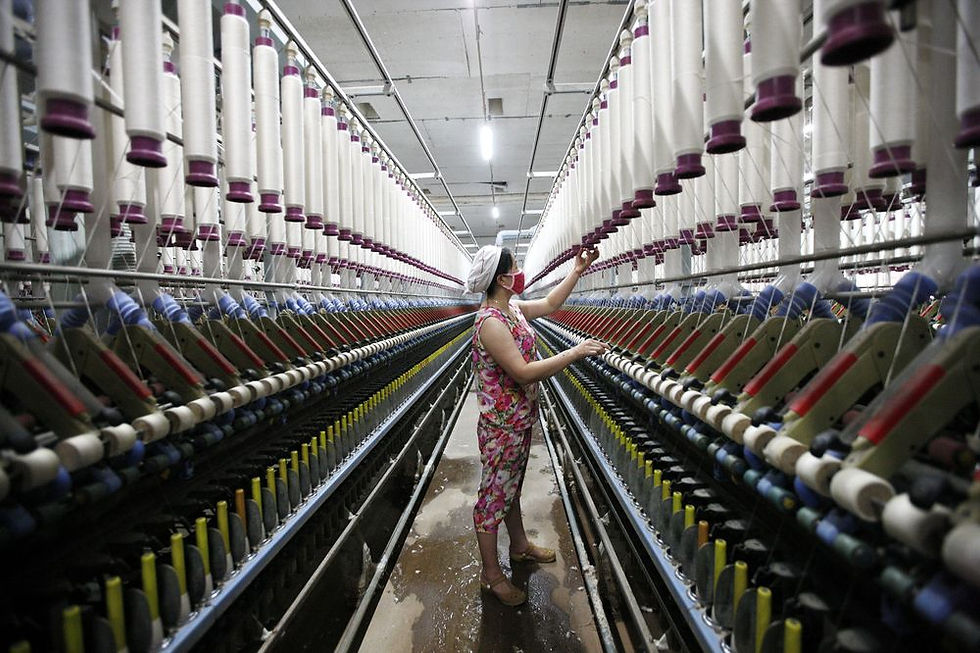
Over the last year, not many factories have opted to move operations to cheaper-wage countries, the survey showed, but instead are investing in robots and automation. About 8 percent of firms now have robots and two-fifths are automated.
“With the reality of rising labor costs and to improve efficiency, we have to keep investing in automation,” says Chen Jiuyuan, the 43-year-old operations manager at Hubei Hengwei Aluminum Co, which produces energy-saving window frames, doors, and car frames, and is also based in Hanchuan. Average line wages have risen from around 2,000 yuan ($292) when Hengwei opened seven years ago, to 3,500 yuan ($512) now, he says.
But while industrial upgrading has been a key strategy, that may be changing. Indeed, fixed capital spending as a proportion of sales fell from 25 percent in 2013 to 19 percent in 2015. Meanwhile, the share of companies investing in R&D has fallen to 44 percent, down ten percentage points since 2014. “Decisions to reduce capital investment are often related to uncertainty about the future. They could reflect views about future growth in China,” says HKUST’s Park.
As the economic environment worsens, one way to keep costs down is to rely on labor service or dispatch companies, rather than hire workers directly. This allows companies to avoid paying the high social welfare payments required by law, amounting to about 40 percent of wages. Also common: county cadres who accept reduced payments to encourage factories to not relocate. The average social insurance contribution for workers runs at just 17% the survey shows. “Companies will negotiate with local officials about how much social welfare contributions they have to put in,” says Wang Kan, a labor expert at the China Institute of Industrial Relations in Beijing.
Most firms are receiving tax exemptions, tax refunds, and outright subsidies, offered by local and provincial administrations eager to encourage industrial upgrading. In Guangdong, there is a subsidy for every robot purchase, for example. Perhaps not surprisingly, state-owned enterprises were the biggest recipients, with 83 percent reporting they receive benefits; for private companies it was just under one-half.
Even with government largess, one fifth of all companies still lose money, with 26% of state-owned firms-eight percentage points more than private ones-in the red. Both the stroller maker and Hengwei Aluminum report they are profitable. “It’s like a baby when it grows too fast gets indigestion,” says Cheng Hong, director of Wuhan University’s quality development institute. “We have discovered that rising labor costs have given us all kinds of problems we didn’t expect.”
Source: Bloomberg
Comments