Metal Injection Molding in Japan: Growth anticipated after a poor 2015
- gtbmsbcs
- 2016年7月22日
- 讀畢需時 2 分鐘
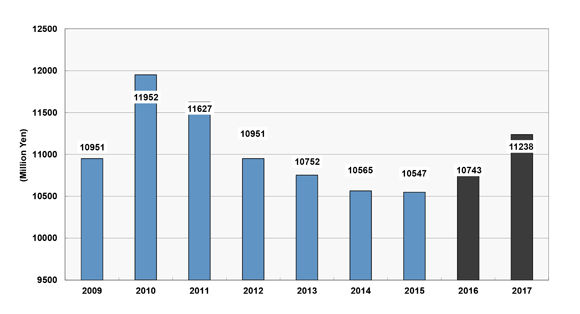
The Japan Powder Metallurgy Association (JPMA) reports that sales of MIM (Metal Injection Molding) parts decreased slightly in 2015 compared with the previous year to reach Yen 10.547 billion (US $99.5 million). This compares with the highpoint of Yen 11,952 billion (US$ 112.8 million) reached in 2010 (Fig. 1). The data is based on the JPMA’s latest annual survey of 21 leading Metal Injection Moulding (MIM) producers in Japan.
However, respondents to the JPMA survey also indicated that Metal Injection Moulding sales would increase over the next two years, reaching Yen 10.743 billion in 2016 and Yen 11,238 billion in 2017.
A breakdown of the application areas for Metal Injection Moulded parts in Japan showed that the Industrial Machine segment remained the largest single sector with a 23.5% market share (down slightly on the previous year), followed by medical appliances which was up one percentage point to 19.3%.

The automotive and motorcycle sectors have been evaluated separately and show market shares of 17.4% and 6.3% respectively, with the motorcycle sector showing a 2.5% gain over the previous year but the automotive sector showing only a 0.1% increase.
The share of the Information Technology sector was shown to be down slightly at 10.7% of the market compared with 11.2% the previous year.
Stainless steel powders still dominate the materials used for MIM parts in Japan with a 65.1% market share. The JPMA reports that stainless steels, ferrous based magnetic materials and Fe-Ni steels account for over 80% of total powder demand for MIM in Japan. The demand for titanium alloy powders for Metal Injection Moulding increased from 1.6% in 2014 to 2.8% in 2015.
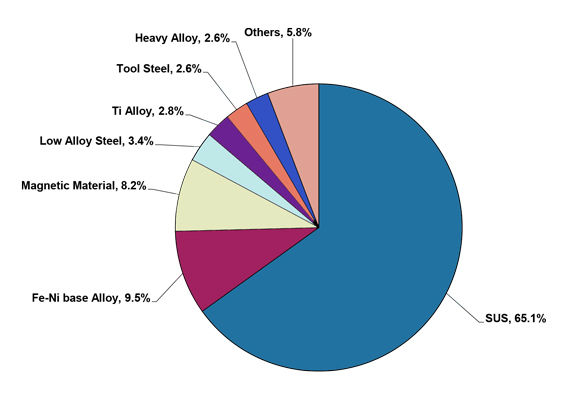
The JPMA reports that it is difficult to predict future trends for Metal Injection Moulding sales in Japan because each MIM producer has different expectations. However, the producers acknowledge that more needs to be done to promote the benefits of Metal Injection Moulding in comparison with other forming technologies.
Comentários